Methods of Prestressing
The prestressing can be performed by two methods:
- Pretensionong
- Post-Tensioning
1. Pretensioning
In the pretensioning method, the stress is induced by initially tensioning the steel tendons. These are wires or strands that are tensioned between the end anchorages. After this tensioning process, the concrete casting is performed.
Once the casted concrete has hardened sufficiently, the end anchorages arranged are released. This releasing transfers the prestress force to the concrete. The bond between the concrete and the steel tendons facilitates this stress transfer.
As shown in figure-2, the tendons that are protruding at the ends are cut and a finished look is achieved. In order to induce prestress force in the pre-tensioning method, a large number of tendons and wires are used. This arrangement hence demands a large area of surface contact to make the bond and stress transfer possible.
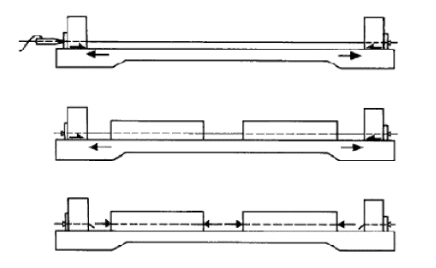
2. Post Tensioning
The procedure in post-tensioning is depicted in the figure-3 below. Here, the steel is prestressed only after the beam is cast, cured and attain strength to take the prestress. Within the sheathing, the concrete is cast. For the passage of steel cables, ducts are formed in the concrete.
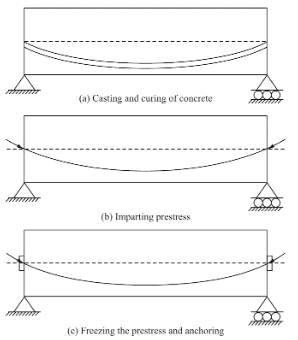
Once the prestressing is complete, there is space between the tendons and the duct. This leads to:
- Bonded Construction
- Unbonded Construction
1. Bonded Construction
In bonded construction, the space between the duct and the tendon is filled with cement grout. The grouting process helps the steel to resist corrosion to a large extent. The ultimate strength is increased as this method increases the resistance to live loads acting. The grout mixture is cement and water combined with or without admixture. No sand is used in this grout.
2. Unbonded Construction
If no grout is used to fill the space between the duct and tendon, it is called as unbonded construction. Here, the steel is galvanized to protect from corrosion. A waterproofing material is used for galvanizing.